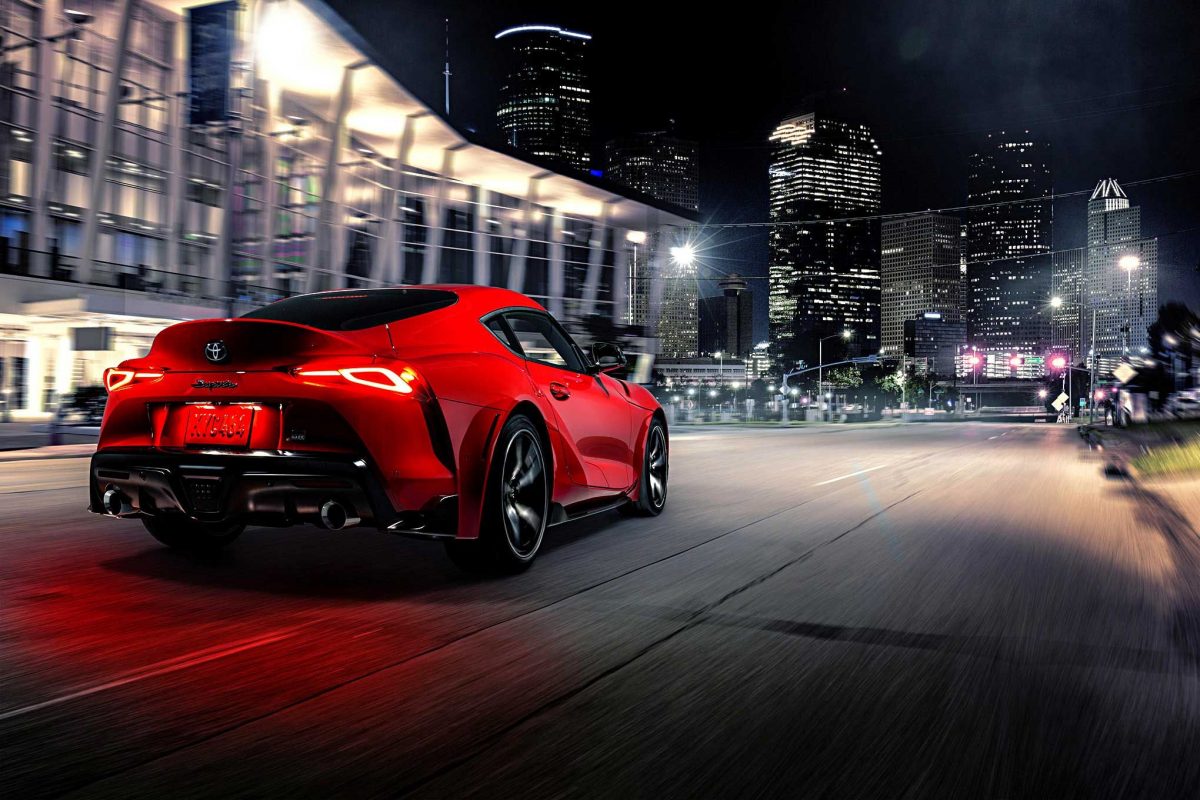
العمليَّات المَرِنَة في شركة تويوتا للسيارات
العمليَّات المَرِنَة في شركة تويوتا للسيارات لـتحقيق ميزة تنافسية ، تعد شركة تويوتا للسيارات -التي تبلغ قيمتها السنوية ٢٥٠ مليار دولار، مع مبيعات سنوية تبلغ ٢٥٠ مليار دولار لأكثر من 9 ملايين سيارة وشاحنة-واحدة من أكبر الشركات المصنعة للسيارات في العالم. هناك أسلوبان مَرِنان -هما استراتيجية “الوقت المناسب” (JIT) ونظام إنتاج تويوتا (TPS)-كانا فعَّالَيْن في نموها. و تتنافس تويوتا، مع مجموعة واسعة من السيارات، وجهاً لوجه مع الشركات الناجحة والراسخة في أوروبا والولايات المتحدة.
Taiichi Ohno، نائب الرئيس السابق لتويوتا، وضع الإطار الأساسي لاثنين من أكثر أنظمة العالم التي نوقشت لتحسين الإنتاجية، و هما “نظام الوقت المناسب” JIT و “نظام تويوتا الإنتاجي” TPS. يوفر هذان المفهومان الكثير من الأساس لمفهوم ” االعمليَّات المَرِنَة”.
محور استراتيجية “في الوقت المناسب “JIT؛ هو فلسفةحل المشاكل المستمرة. في الممارسة العملية، JITتعني صنع ما هو مطلوب فقط، عند الحاجة إليه. وتوفر JIT وسيلة ممتازة للعثور على المشاكل والقضاء عليهالأن المشاكل يسهل العثور عليها في نظام يلغي الركود الذي يولده المخزون. عندما يتم التخلص من المخزون الزائد، تصبح أوجه القصور المتعلقة بالجودة والتخطيط والجدولة وأداء الموردين واضحة على الفور – كما هو الحال بالنسبة للإنتاج الزائد.
من الأمور الأساسية في نظام إنتاج تويوتا “TPS” هو تعلم الموظف، والاستمرار في توفير الكثير من الأساس لجهد المرونة “leaning effort” لإنشاء وإنتاج المنتجات في ظل ظروف مثالية. لا توجد ظروف مثالية إلا عندما تجمع الإدارة المرافق والآلات والأفراد معًا لإضافة قيمة دون إهدار. فالمُهْدَرات تقوِّض الإنتاجية عن طريق: تحويل الموارد إلى فائض في المخزون، والمعالجة غير الضرورية، والنوعية الرديئة.
استخدمت المكاتب ومتاجر البيع بالتجزئة، وكذلك الشركات المصنعة 5Ss بنجاح في جهودهم الخاصة للقضاء على النفايات والانتقال إلى العمليَّات المَرِنَة . وجود مكان لكل شيء ووجود كل شيء في مكانه يُحدث فرقًا في مكتب جيد الإدارة. تستخدم متاجر البيع بالتجزئة Ss بنجاح لتقليل البضائع غير الصالحة وتحسين خدمة العملاء. يعمل مكان العمل المنظم على تقليل الإهدار وإطلاق الأصول لأغراض أخرى أكثر إنتاجية.
إزالة التبايُن:
يسعى المديرون إلى إزالة التباين الناجم عن كل من العوامل الداخلية والخارجية وهو أي انحراف عن العملية المثلى التي توفر منتجًا مثاليًا في الوقت المحدد، في كل مرة. التغير هو كلمة مهذبة للمشاكل. كلما قلَّ التبايُن في النظام، كلما قلَّ الإهدار فيه. ومعظم التباينات ناتجة عن التساهُل مع الإهدار، أو عن سوء الإدارة.
من بين العديد من مصادر التباين:
- العمليَّات ضعيفة المستوى التي تسمح للموظفين والموردين بإنتاج كميات غير مناسبة أو إنتاج وحدات غير مطابقة.
- الصيانة غير الملائمة للمنشآت العمليَّات .
- متطلبات العملاء غير المعروفة والمتغيرة.
- التصاميم غير الكاملة أو غير الدقيقة، والمواصفات، وفواتير المواد الخام.
ويعتبر خفض المخزون عن طريق JIT أداة فعالة لتحديد أسباب التباين. والتوقيت الدقيق لـ JIT يجعل التباين واضحًا، تماماً كما يكشف تقليص المخزون عن التباين. إن التغلب على التباين يتيح للمديرين نقل المواد الجيدة حسب الجدول الزمني، وإضافة القيمة في كل خطوة من خطوات العملية، وخفض التكاليف، وفي النهاية الفوز تلبية الطلبات.
إنجاز استراتيجيَّتَيّ JIT وTPS :
يظهر إنجاز استراتيجيَّتَيّ JIT وTPS في تويوتا من خلال منشأتها في سان أنطونيو، تكساس، التي تبلغ مساحتها ٢٠٠٠ فدان، وهو أكبر موقع لتويوتا على الأرض كمصنع لتجميع السيارات في الولايات المتحدة.
من المثير للاهتمام، على الرغم من موقعها الكبير وقدرتها الإنتاجية السنوية البالغة ٢٠٠٠٠٠، وهو وقت إنتاج يبلغ ٢٠ ساعة ونصف، وإخراج شاحنة كل 63 ثانية، يعد المبنى نفسه من أصغر المباني في هذه الصناعة. تحتوي السيارات الحديثة على ٣٠٠٠٠ قطعة، ولكن في شركة تويوتا، يجمع الموردون المستقلون بين العديد من هذه الأجزاء في مجموعات فرعية. يوجد ٢١ من هؤلاء الموردين في الموقع في منشأة سان أنطونيو ويقومون بنقل المكونات إلى خط التجميع على أساس JIT.
هذه العمليات التي تجري في مصنع سان أنطونيو هي السبب وراء استمرار أداء تويوتا بالقرب من أعلى مستويات الجودة والحفاظ على أقل وقت للتجميع في ساعات العمل في هذه الصناعة. العمليَّات المَرِنَة تؤدي العمل وهي توفر ميزة تنافسية لشركة تويوتا للسيارات.
تعريف العمليَّات المَرِنَة
كما هو موضح في ملف تعريف الشركة العالمي، فإن نظام إنتاج تويوتا (TPS) يساهم في عملية عالمية المستوى في شركة تويوتا موتور. في هذا المقال، نناقش العمليَّات المَرِنَة ، بما في ذلك JIT وTPS، كطرق للتحسين المستمر التي تؤدي إلى عمليات ذات مستوى عال .وهي مدفوعة بسَيْر العمل الذي بدأ بـ “سحب” طلب العميل.
“في الوقت المناسب” أو (JIT) هو نهج لحل المشاكل بشكل مستمر وإجباري من خلال التركيز على الإنتاجية وانخفاض المخزون. و يعتبر نظام إنتاج تويوتا أو(TPS)، مع التركيز على التحسين المستمر واحترام الأفراد وممارسات العمل القياسية، مناسبًا بشكل خاص لخطوط التجميع.
في هذا المقال، نستخدم مصطلح عمليات مَرِنَة ليشمل جميع الأساليب والتقنيات ذات الصلة لكل من JIT وTPS. عند تنفيذها كاستراتيجية شاملة للعمليات، تحافظ على الميزة التنافسية وتؤدي إلى زيادة العوائد الإجمالية لأصحاب المصلحة.
بغض النظر عن النهج والتسمية، يعالج مديرو العمليَّات ثلاث قضايا أساسية لتحسين العمليَّات : التخلص من المُهْدَرات، وإزالة التباين، وتحسين الناتج. نعرض الآن هذه المشكلات .
القضاء على النفايات
وضع المنتجون المَرِنون نظرتهم عن الكمال على أنه: عدم وجود أجزاء سيئة، وعدم وجود مخزون، يوجد فقط أنشطة ذات قيمة مضافة، ولا يوجد مُهْدَرات. أي نشاط لا يضيف قيمة في نظر العميل؛ فهو إهدار. فيحدد العميل قيمة المنتج. إذا كان العميل لا يريد أن يدفع ثمنه، فهذا إهدار. “تايشي أوهنو” – المعروف بعمله في نظام إنتاج تويوتا- حدد سبع فئات من النفايات. أصبحت هذه الفئات شائعة في منظمات المرونة وتغطي العديد من الطرق التي تهدر بها المنظمات أو تخسر المال. و مُهدرات أوهنو السبعة هي:
- الإنتاج الزائد: إنتاج أكثر من طلبات العملاء أو الإنتاج المبكر (قبل الطلب) هو إهدار.
- الطوابير: الوقت الضائع والتخزين والانتظار هي مُهدَرات (لا تضيف أي قيمة).
- النقل: يعد نقل المواد بين المصانع أو بين مراكز العمل والتعامل معها أكثر من مرة إهدارًا.
- المَخزون: المواد الخام غير الضرورية، والمواد الجاري العمل عليها (WIP)، والسلع تامة
الصنع، واللوازم التشغيلية الزائدة لا تضيف قيمة وهي مُهدَرات. - الحركة: حركة المعدات أو الأشخاص الذين لا يضيفون أي قيمة هي إهدار.
- المعالجة الزائدة: العمل الذي لا يضيف أي قيمة على المنتج هو إهدار.
- المنتج المعيب: تعتبر عمليات الإرجاع ومطالبات الضمان وإعادة العمل والخردة مُهْدرات.
إن المنظور الأوسع نطاقًا – الذي يتجاوز الإنتاج الفوري – يشير إلى أن الموارد الأخرى، مثل الطاقة والمياه والهواء، غالباً ما تُهدر ولكن هذا لا يجب أن يحدث. كفاءة الإنتاج المستدام تقلل المدخلات وتزيد من المخرجات، بدون أي إهدار.
على مدار أكثر من قرن من الزمان، اتبع المديرون استراتيجيَّة “إدارة الممتلكات الخماسيَّة” من أجل مكان عمل أنيق ومُنظم وفعال وكوسيلة للحد من المُهْدرات. قام مديرو العمليَّات بتنميق “إدارة الممتلكات الخُماسيَّة” ليشمل قائمة مراجعة معروفة الآن باسم 5Ss. طور اليابانيون 5Ss الأولي. 5Ss ليست فقط قائمة مراجعة جيدة للعمليات المَرِنَة ، ولكنها توفر أيضًا وسيلة سهلة للمساعدة في تغيير الثقافة التي غالبًا ما تكون ضرورية لتحقيق العمليَّات المَرِنَة .
تقنيات إدارة الممتلكات ( 5Ss )
- افرز / افصل Sort: حافظ على ما هو مطلوب وأَزِلْ كل شيء آخر من منطقة العمل؛ عندما تكون في
شك، ارمِه خارجًا. حَدِّد العناصر غير القيِّمة وأزِلْها. يتيح التخلص من هذه العناصر توفير مساحة وعادة ما يُحسِّن سير العمل. - بسِّط / قَوِّم Simplify: رَتِّب واستخدم أدوات تحليل الأساليب لتحسين سير العمل وتقليل الحركة
المهدرة. ضع بعين الاعتبار متعلقات بيئة العمل المريحة على المدى الطويل والقصير. عَنوِنْ وأتِحْ للاستخدام السهل ما هو مطلوب فقط في منطقة العمل المباشرة. - لَمِّع / نَظِّف Shine: نَظِّف يوميًّا، وتخلص من جميع أشكال الأوساخ والتلوث والفوضى من منطقة العمل.
- عايِر / وَحِّد Standardize: أزِلْ الاختلافات من العملية من خلال تطوير إجراءات التشغيل و
قوائم المراجعة القياسية؛ المعايير الجيدة تجعل غيرَ الطبيعي واضحًا. قم بتوحيد المعدات والأدوات
بحيث يتم تقليل وقت التدريب المتبادل والتكلفة. قم بتدريب فريق العمل وإعادة تدريبه حتى تظهر الانحرافات بسهولة عند حدوث الانحرافات. - الاستدامة / الانضباط الذاتيSustain: قم بمراجعة دورية للتعرف على الجهود والتحفيز للحفاظ
على التقدم. استخدم الصور المرئية كلما أمكن ذلك للتواصل والحفاظ على التقدم.
غالبًا ما يضيف المدراء الأمريكيون اثنتَين إضافيتين في قائمة Ss تساهمان في إنشاء وصيانة مكان
عمل مَرِن:
- السلامة Safety: اِبْنِ ممارسات سلامة جيدة في الأنشطة الخمسة السابقة.
- الدعم / الصيانة Support/maintenance: قَلِّلْ التباين، والتوقف غير المخطط له، والتكاليف. و
ادمج مهام التلميع / التأنُّق اليومية مع الصيانة الوقائية.
تدعم Ss التحسين المستمر وتوفر وسيلة يمكن للموظفين التعرف عليها. يحتاج مديرو العمليَّات إلى التفكير فقط في الأمثلة التي وضعتها غرفة الطوارئ في المستشفيات والتي تُدار بشكل جيد، أو تقنية “التنظيف والتلميع” لقسم مكافحة الحرائق للحصول على معيار واضح.
استخدمت المكاتب ومتاجر البيع بالتجزئة، وكذلك الشركات المصنعة 5Ss بنجاح في جهودهم الخاصة للقضاء على النفايات والانتقال إلى العمليَّات المَرِنَة.
وجود مكان لكل شيء ووجود كل شيء في مكانه يُحدث فرقًا في مكتب جيد الإدارة. تستخدم متاجر البيع بالتجزئة 5Ss بنجاح لتقليل البضائع غير الصالحة وتحسين خدمة العملاء.
يعمل مكان العمل المنظم على تقليل الإهدار وإطلاق الأصول لأغراض أخرى أكثر إنتاجية.
إزالة التبايُن:
يسعى المديرون إلى إزالة التباين الناجم عن كل من العوامل الداخلية والخارجية وهو أي انحراف عن العملية المثلى التي توفر منتجًا مثاليًا في الوقت المحدد، في كل مرة. التبايُن هو كلمة مهذبة للمشاكل. كلما قلَّ التبايُن في النظام، كلما قلَّ الإهدار فيه. ومعظم التباينات ناتجة عن التساهُل مع الإهدار، أو عن سوء الإدارة.
من بين العديد من مصادر التباين:
- العمليَّات ضعيفة المستوى التي تسمح للموظفين والموردين بإنتاج كميات غير مناسبة أو إنتاج وحدات غير مطابقة.
- الصيانة غير الملائمة للمنشآت والعمليَّات .
- متطلبات العملاء غير المعروفة والمتغيرة.
- التصاميم غير الكاملة أو غير الدقيقة، والمواصفات، وفواتير المواد الخام.
ويعتبر خفض المخزون عن طريق JIT أداة فعالة لتحديد أسباب التباين. والتوقيت الدقيق لـ JIT يجعل التباين واضحًا، تماماً كما يكشف تقليص المخزون عن التباين. إن التغلب على التباين يتيح للمديرين نقل المواد الجيدة حسب الجدول الزمني، وإضافة القيمة في كل خطوة من خطوات العملية، وخفض التكاليف، وفي النهاية الفوز بتلبية الطلبات.
تحسين الإنتاجية
الإنتاجية هي معدل تحرك الوحدات خلال العملية. فكل دقيقة تبقى فيها المنتجات في سجل الأعمال، تتراكم التكاليف، وتضيع الميزة التنافسية، فالوقت من ذهب. يطلق على الوقت الذي يوجد فيه الطلب في المتجر “وقت دورة التصنيع”. هذا هو الوقت الفاصل بين وقت وصول دورة تصنيع المواد الخام وشحن المنتج النهائي. على سبيل المثال، كانت شركة تصنيع أنظمة الهاتف Nortel تحتوي على مواد تم سحبها مباشرةً من موردين مؤهلين إلى خط التجميع.
هذا الجهد خفَّض قِسمًا من وقت دورة التصنيع من 3 أسابيع إلى 4 ساعات فقط، وخَفَّضَ موظفي تفتيش الواردات من 47 إلى 24، والمشاكل في أرضية المتجر الناجمة عن المواد المعيبة بنسبة 97 ٪. فيُمكن أن يؤدي انخفاض وقت دورة التصنيع إلى حدوث تحسن كبير في الإنتاجية.
نظام السحب :
نظام السحب هو تقنية لزيادة الإنتاجية. فيسحب نظام السحب وحدة إلى حيث تكون هناك حاجة إليها تمامًا كما هو مطلوب. نظام السحب هو أداة قياسية للمرونة. تستخدم أنظمة السحب إشارات لطلب الإنتاج والتسليم من محطات الإمداد إلى المحطات التي لديها طاقة إنتاجية متاحة. و يتم استخدام مفهوم السحب في كل من عملية الإنتاج المباشرة ومع الموردين.
إن سحب المواد خلال عملية الإنتاج كما هو مطلوب بدلاً من وضع “الدفع” يؤدي عادةً إلى خفض التكلفة و تحسين أداء الجدول، مما يعزز رضا العملاء.